Aplicaciones
Inspección UTPA de baja frecuencia de GFRP
Publicado
hace 4 añoson
By
kresko-admin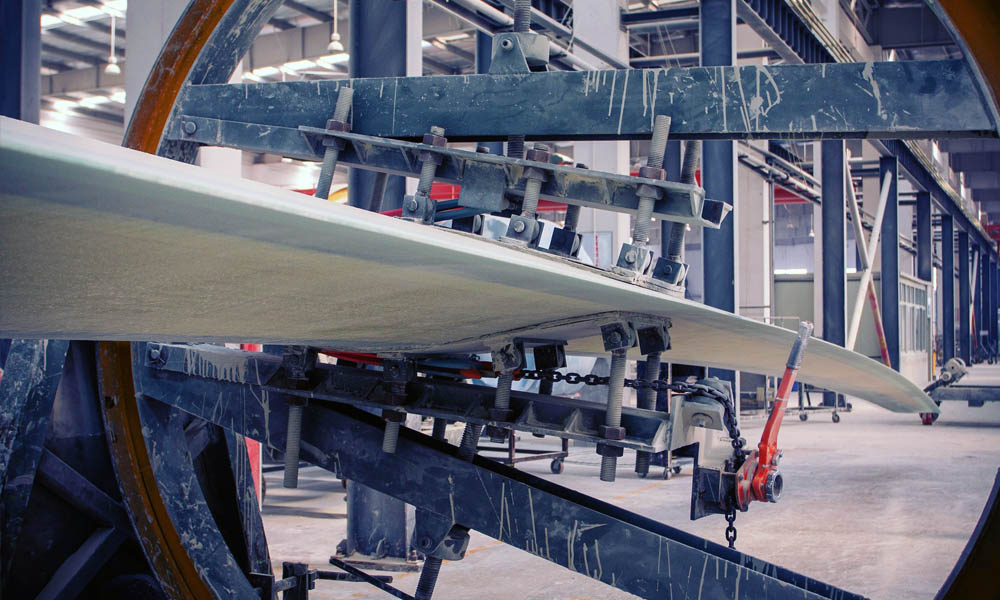
Industrias: Oil & Gas, Petroquímica, Generación de energía
Aplicaciones típicas: Bridas, Barras, hélices de turbina eólica, Cascos de barcos
Técnica de inspección: Barrido C codificado Arreglo de fases, Técnica basada en amplitud
En esta nota de aplicación nos centraremos en la inspección de plásticos reforzados con fibra de vidrio (GFRP), específicamente los utilizados en la fabricación de palas de aerogeneradores. Los defectos comunes en este material incluirán huecos / burbujas de aire atrapados en el epoxi (porosidad), deslaminaciones entre las capas de fibra, especialmente alrededor de áreas con cambios de espesor y daño al larguero debido a un exceso de tensión en las palas.
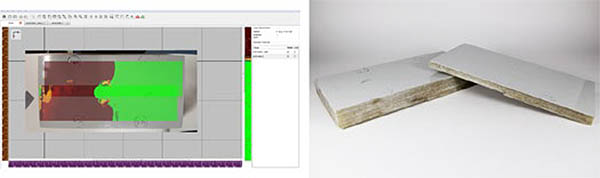
Inspección UTPA de baja frecuencia de GFRP
Características y beneficios
- Mayor cobertura de inspección
- Reducción del tiempo, ya que la inspección se puede realizar
- mientras las hélices están en la turbina.
- Mayor penetración utilizando un transductor de baja frecuencia
- Ligero y portátil
- Excelente señal / ruido para una imagen más clara
Procedimiento de inspección
El procedimiento de prueba se demostró en dos muestras como se muestra a continuación, las piezas que se inspeccionan son secciones de una pala de turbina eólica, ambas secciones tienen 2 espesores diferentes, 18,5 mm, 23,5 mm, 41,5 mm y 46,4 mm.
Los defectos comienzan en el área donde cambia el grosor y continúan hasta el lado más
grueso de las muestras.
Esquemas prácticos
Necesidad de una inspección con arreglo de fases
- La necesidad de inspección de las palas de las turbinas eólicas comienza en su fabricación y continúa a lo largo de su vida útil, ya que cada pala se somete a diferentes tensiones de su entorno.
- Durante el proceso de fabricación, puede producirse una delaminación, estos defectos a menudo se ocultan a la vista y necesitan ser inspeccionados por ultrasonidos. Las áreas comunes para la delaminación son alrededor de orificios perforados (para sujetadores) y alrededor de bordes / cambios de espesor.
- Otro defecto que se puede introducir durante la fabricación es la porosidad, se trata de un área o aire / aire.
- Burbujas que quedan atrapadas durante el proceso de inyección y curado de la resina.
- Durante la vida útil de una pala de aerogenerador, se deben realizar inspecciones para ayudar a descubrir nuevos defectos que puedan formarse, estos pueden incluir:
- Separación del larguero debido a un alto estrés.
- Daño por impacto de aves.
- Delaminación causada por demasiada flexión de las cuchillas durante el funcionamiento durante vientos fuertes.
Beneficios de la inspección
Las palas de las turbinas eólicas son artículos de alto valor, también son difíciles de transportar y cambiar. Por lo tanto, es muy importante que se realicen las inspecciones adecuadas, reduciendo la necesidad de cambiar las cuchillas innecesariamente y evitando fallas en el servicio. Con este método de prueba, la inspección se puede realizar mientras las palas están unidas a la turbina mediante un acceso por cuerda, lo que significa que no es necesario quitar las palas y llevarlas a una ubicación en el suelo, lo que reduce el costo y el tiempo de inactividad general.
No toda la delaminación serán fallas, al usar una matriz en fase, es fácil monitorear cualquier crecimiento en el tamaño de la delaminación, por lo tanto, se encuentra el momento adecuado para quitar o reparar la pala de la turbina.
La delaminación, las arrugas, el dimensionamiento y la caracterización de la porosidad se mejoran con UTstudio + e incluso se pueden dimensionar automáticamente con la anotación única de UTmap.
Conclusión
El transductor de matriz en fase de baja frecuencia de Sonatest, junto con una de nuestras unidades rápidas y capaces, proporciona una forma fácil de usar y confiable de garantizar una inspección minuciosa de NDT de las palas de las turbinas eólicas.
Debido a la versatilidad de nuestras unidades, se pueden realizar muchas otras inspecciones relacionadas con las turbinas eólicas, por ejemplo las soldaduras en los soportes así como la verificación de corrosión en áreas específicas.
Aplicaciones
Inspección de Puntos de Soldadura Spotweld
Publicado
hace 4 añoson
octubre 7, 2021By
kresko-admin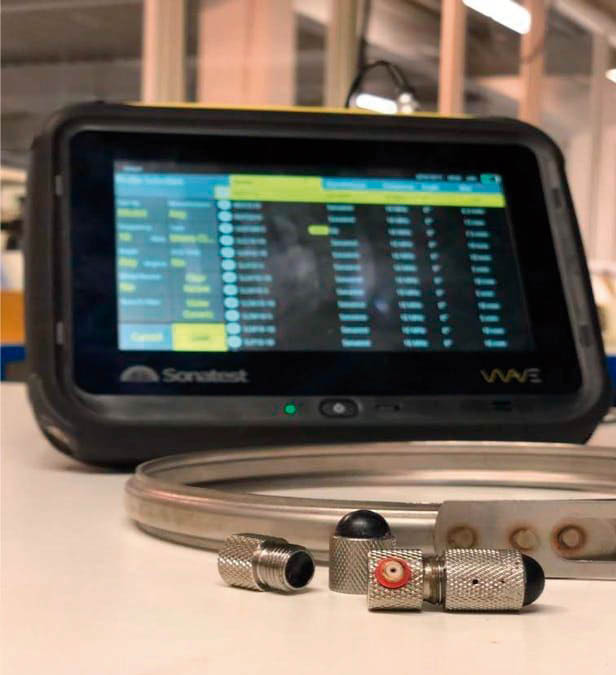
Industrias: Automotriz, Fabricación, Aeroespacial, Construcción, Ferroviaria.
Partes Típicas: Chasis, Rieles, Baterías, Chapas, Malla de alambre (Malla soldada).
Características y Beneficios: Fácil de actualizar, Inspecciones rápidas y confiables, Reducción de costos, Procedimiento de ejecución simple.
Paquete Recomendado: Equipo de Ultrasonido Wave o D-70, Transductor RB2010 10 MHz, Spot weld ball de 10 mm, 151631 y 151635.
APLICACIÓN
Evaluación de la integridad de uniones de soldaduras por puntos en metales.
La soldadura por puntos es una técnica comúnmente utilizada para unir dos piezas metálicas, generalmente, laminas, mediante una soldadura que hace que estas laminas se adhieran entre sí de manera instantánea, generalmente esta soldadura presenta una morfología circular. Este proceso es usado ampliamente en la industria automotriz para el montaje de la carrocería y
algunas uniones del chasis y, también, por otros fabricantes de láminas o chapas metálicas.
Las soldaduras por puntos se realiza haciendo pasar una corriente eléctrica a través de dos electrodos que presionan las láminas que se desea unir, esta corriente al ser de alta energía genera altas temperaturas en las láminas fundiendo el material de la zona en la que se encuentra la presión ejercida por los electros, al retirar la presión de los electrodos el material fundido solidifica de manera instantánea generando así un empalme de forma circular, a este empalme se le conoce como punto de soldadura o núcleo de soldadura.
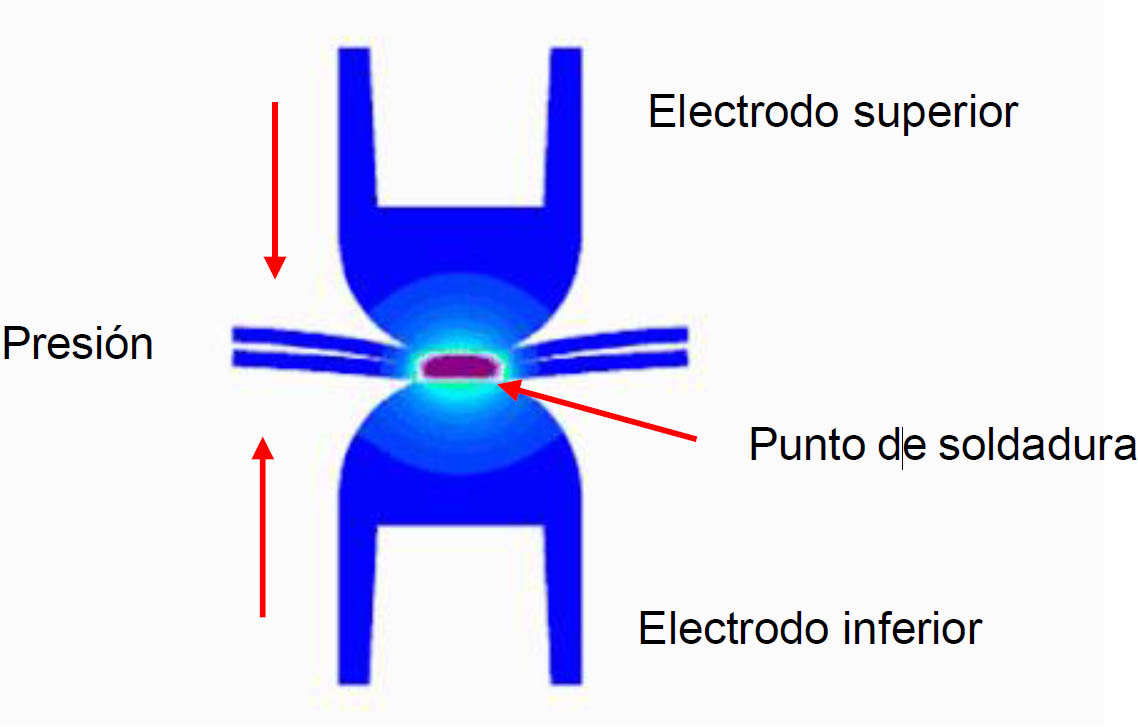
diagrama soldaduras por puntos
Es importante mencionar que en caso que esta soldadura no sea realiza de forma adecuada, las piezas de interés no tengan una buena unión (fusión incompleta), o que el punto de soldadura sea más pequeño de lo que se requiere para asegurar una unión resistente. Estos problemas suelen ser visibles mediante inspecciones visuales; otra forma de garantizar una unió
uniforme es realizar pruebas de estiramiento las cuales son técnicas destructivas, aunado a esto se consideran ineficaces y se limitan a ciertas muestras. No obstante, con el equipo y la técnica adecuada, la inspección por ultrasonido en soldaduras por puntos proporciona información valiosa de manera rápida y no destructiva acerca de la calidad de la soldadura.
De esta forma podemos clasificar de maneras distintas los puntos de soldadura como:
• GOODWELD
• UNWELD
• UNDERSIZED
• STICK WELD
Equipo para inspección de
puntos de soldadura Spotweld
El equipo recomendado para inspeccionar puntos de soldadura, puede ser el detector de fallas WAVE O D-70 de la marca Sonates. Las inspecciones de puntos de soldaduras requieren
de transductores de altas frecuencias, así como de línea de retardo de forma cónica la cual garantice un acoplamiento homogéneo sobre el punto a inspeccionar por lo cual se
recomienda utilizar zapatas con diámetros de contacto de 3 a 6 mm (de 0,125 a 0,250 in).
Las puntas de goma de los transductores Sonatest están diseñadas para ser usadas con la familia de línea de retardo RDT y ofrecen una alternativa efectiva al enfoque más tradicional de los transductores de contacto de burbuja de agua.
Estos tienen una mejor expectativa de vida a diferencia de los transductores que cuentas con puntas de burbuja de agua y el uso del caucho reduce drásticamente la cantidad de acoplante
requerido para garantizar un buen contacto. Considerando que las superficies flexibles trabajan excepcionalmente bien en superficies irregulares.
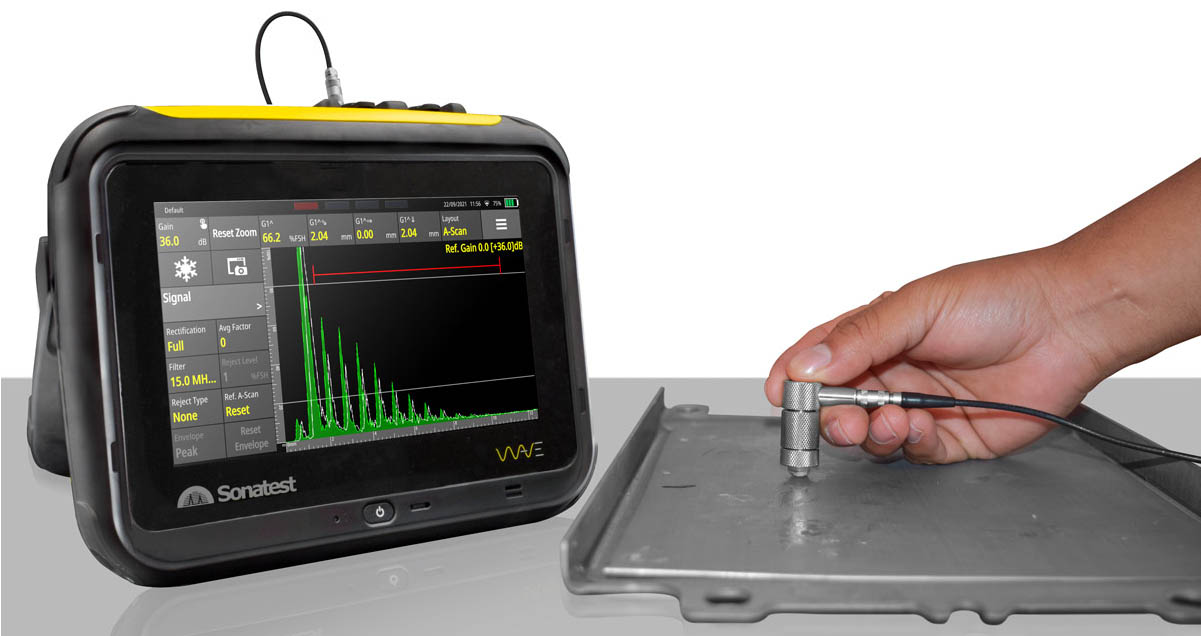
Detector de fallas Ultrasónico WAVE
GOODWELD
En una soldadura correcta, la distancia entre los ecos será proporcional al espesor de la soldadura y la velocidad de caída (es decir, la velocidad por la cual los ecos disminuyen en amplitud) estará relacionada con la atenuación en el núcleo. Figura 1

Fig. 1 Barrido A Scan que muestra una buena unión entre placas (unión completa)
UNWELD
De no existir fusión entre las dos piezas metálicas, Una placa con una soldadura no realizada correctamente conduce a una secuencia de ecos largos con intervalos de ecos cortos correspondientes al espesor de la placa (superior). Figura 2
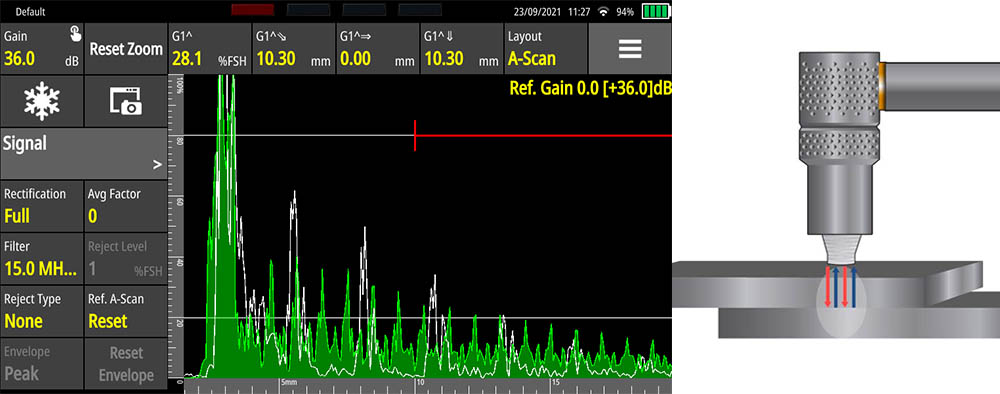
Fig. 2 B arrido A Scan que muestra el espesor de solo una lámina debido a una nula soldadura.
UNDERSIZED
En el caso de una soldadura de tamaño reducido, solo una porción del haz acústico será reflejada a partir del espesor total de las dos láminas de metal, mientras otra porción será reflejada a partir de un solo espesor. En el barrido A visualizaremos ecos pequeños, que representan el espesor de una sola lámina, estos tendrán lugar entre los ecos más grandes y de mayor separación, lo cual representa el espesor total de la soldadura. Figura 3
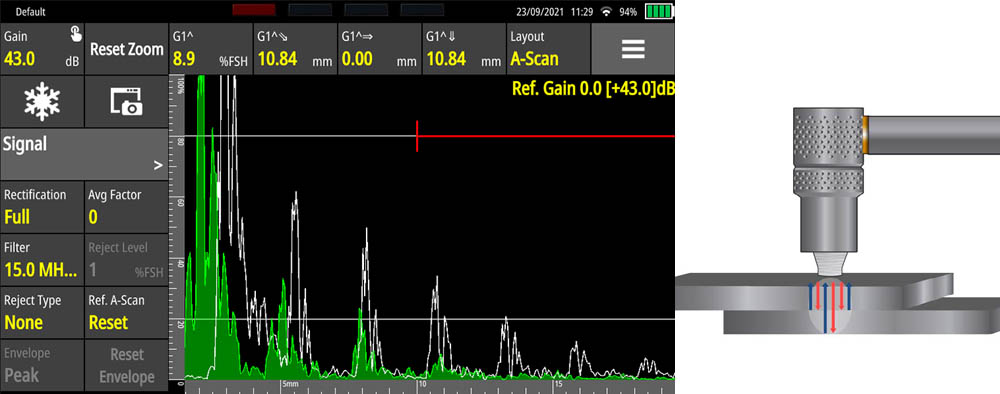
Fig. 3 Barrido A Scan ecos pequeños, que representan el esp esor de una sola lámina,
estos tendrán lugar entre los ecos más grandes y de mayor separación, lo cual representa
el espesor total de la soldadura
STICK WELD
Finalmente, en una condición de falta de adherencia (donde las láminas metálicas no son fusionadas; debido al calor insuficiente, la formación del núcleo de la soldadura no se lleva a cabo), la velocidad de caída del eco cambiará. Los ecos generados serán más grandes con un tiempo de reverberación «ring-down» más amplio, por lo que el material de soldadura es altamente atenuador debido a que posee una estructura de grano más gruesa. Esto lleva a que el ultrasonido transmitido disminuya rápidamente debido a la mayor atenuación. Figura 4
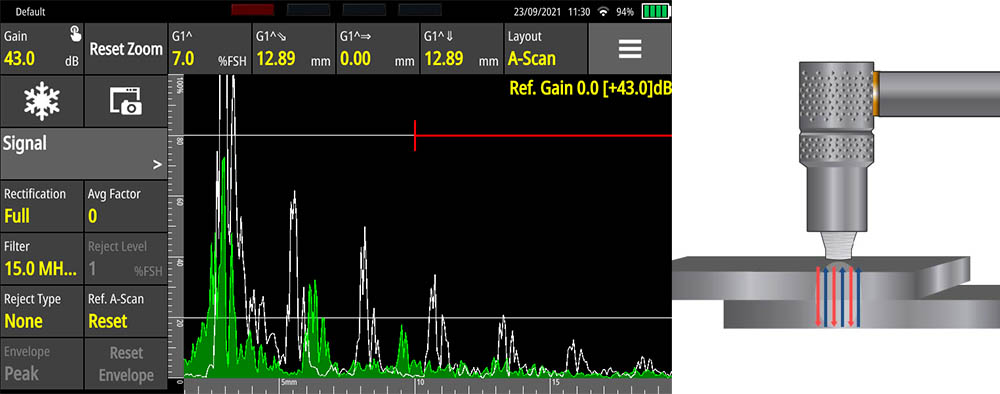
Fig. 4 Barrido A Scan que muestra la falta de adherencia entre las placas, los ecos generados serán
más grandes más amplios, por lo que el material de soldadura es altamente atenuador
Conclusión
Las pruebas manuales pueden ser muy efectivas para detectar condiciones de soldadura “defectuosas” asociadas con el proceso de unión de soldadura por puntos. Esto siempre depende del operador y necesita una buena comprensión de los principios ultrasónicos. El principal beneficio de las pruebas manuales es principalmente el bajo costo y la portabilidad en comparación con los sistemas fijos o robóticos más grandes.
Aplicaciones
Inspección de soldadura en tubos, tuberías o superficies curvas
Publicado
hace 4 añoson
octubre 7, 2021By
kresko-admin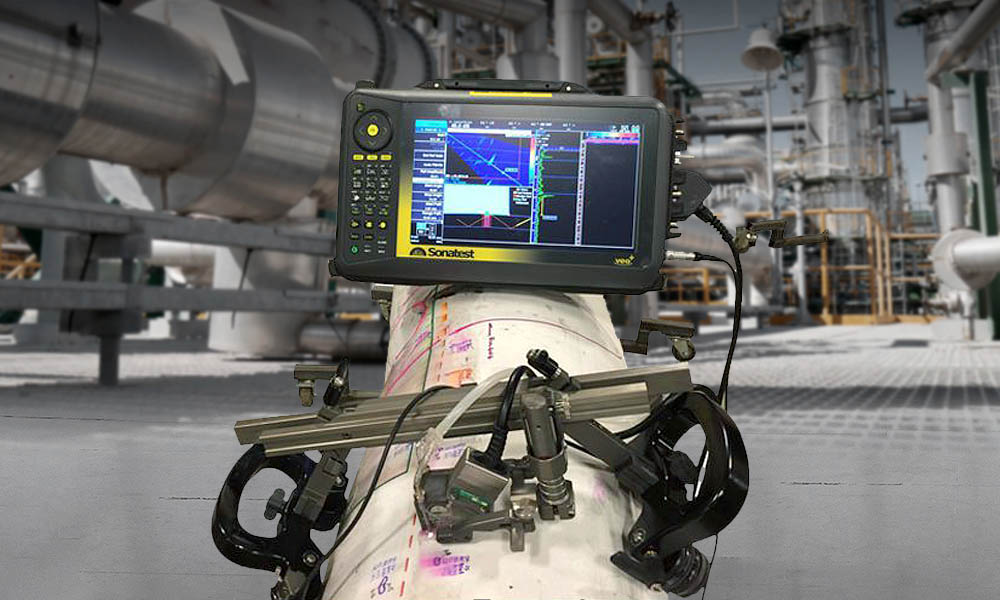
Corrección de Superficie Curva (csc) para inspección de soldadura larga
La inspección por arreglo de fases de soldadura larga en componentes curvos como tubos y tuberías puede ser desafiante, especialmente para costuras de soldadura en diámetros pequeño o tubos de pared gruesa ya que los softwares de inspección, herramientas y accesorios son generalmente diseñados para superficies planas.
Además de que la interpretación del escáner puede ser difícil para ciertas circunstancias, debido a la geometría convexa de la superficie y en muchos casos las herramientas de la visualización de sobre posiciones en soldaduras no son relevantes. El resultado es erróneo frecuentemente, la localización y dimensionamiento del defecto no es preciso en la inspección de soldadura en tubos, tuberías o superficies curvas.
Ésta aplicación destaca un nuevo enfoque en la inspección de costuras soldadas usando el software PA-CSC de veo 3 Sonatest. Una vez que la región o regiones de interés en la soldadura han sido definidas por el inspector, se realiza un enfoque automático en la región. Los S-Scans rápidos pueden ser grabados con la ayuda de un escáner apropiado. Por otra parte, las vistas corregidas del A-Scan son producidas y soportadas por un escaneo en vivo 3D así el técnico puede realizar una identificación, interpretación, medición y dimensionamiento del defecto.
1. Desafíos con arreglo de fases en Inspección de soldadura en tubos, tuberías o superficies curvas.
Configurar un escáner PAUT con recubrimiento representando la soldadura es muy común. En el caso de superficies planas, el usa un salto para lidiarlo con la señal del sonido representando el recubrimiento de la soldadura. En el caso de superficies curvas, éste método no puede ser usado como se aprecia en las imágenes recolectadas, en la superficie convexa se distorsiona y la superficie no puede ser examinada. Además, la profundidad medida del defecto cambiaría a medida que la sonda viaja a lo largo de la superficie curva.
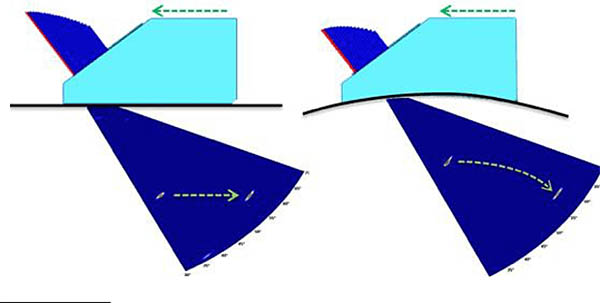
arreglo de fases en superficies curvas
Actualmente, el objetivo de la mayoría de las inspecciones de soldaduras de costura larga es detectar daños mecánicos en servicio. La nitidez y la resolución de la imagen es crítica para tales evaluaciones cuando se trata de la caracterización de un defecto. De hecho, el desfase de la caracterización puede resultar en una reparación innecesaria en defectos de fabricación ya aceptados.
2. Solución de enfoque de resolución
Cuando se utiliza el método tradicional de enfoque de trayectoria constante en superficies curvas, los puntos de enfoque se ven afectados por el efecto de lente convexo en el segundo salto, disminuyendo significativamente el ángulo de resolución, la densidad de energía del haz y la nitidez de la imagen que conduce a una baja probabilidad de detección.
El nuevo enfoque de resolución constante PA-CSC permite al usuario definir una resolución de haz fija en la región de interés, se usa este parámetro para que el generador de ley focal genere haces UT en ángulos específicos para garantizar una cobertura completa de la soldadura y la densidad del haz, teniendo en cuenta los efectos de la superficie curva. Además, la profundidad de falla real ahora se calcula a partir de los A-Scan corregidos y no es afectado por la ubicación de la sonda. Esta característica está agregada en el instrumento.
Aquí están los resultados de dos patrones focales diferentes, del lado izquierdo siguiendo un camino constante y del lado derecho una resolución constante.
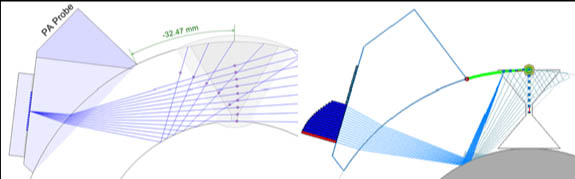
resultados de dos patrones focales diferentes, del lado izquierdo siguiendo un camino constante y del lado derecho una resolución constante
Como se muestra en la figura de abajo, se puede ver fácilmente que el método asegura el enfoque y la optimización de la imagen para la región de interés definida por el inspector, asegurando la apropiada y precisa localización del defecto con arreglo de fases.
Se puede establecer un enlace estable entre el A-Scan, el escáner sectorial y la vista 3D en vivo proporcionando asistencia invaluable para permitir al técnico localizar y dimensionar los defectos con seguridad. También es posible hacerse un análisis posterior usando el software UT Studio para extraer y analizar datos, crear reportes y compartir información.
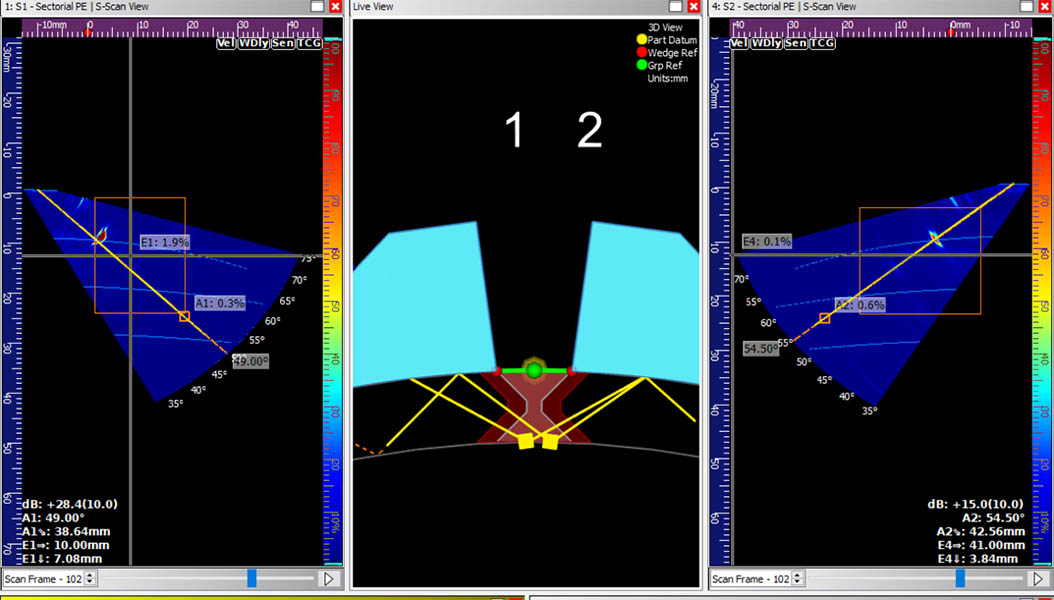
A-Scan, el escáner sectorial y la vista 3D en vivo
Al desarrollar y probar la capacidad de la constante resolución de enfoque, Sonatest provee un método único, fácil de usar y preciso para la evaluación de soldaduras en costuras.
Aplicaciones
Inspección de Soldaduras Estructurales por AWS
Publicado
hace 4 añoson
octubre 5, 2021By
Saraí Bello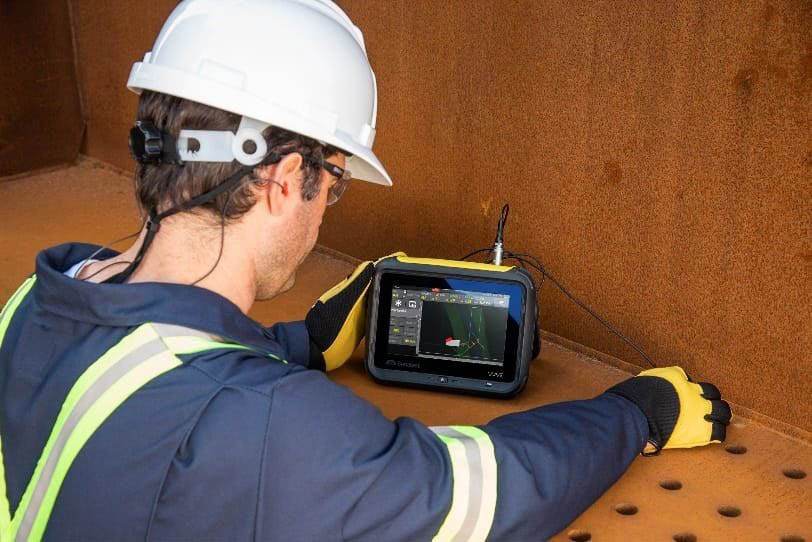
Industrias: Soldadura estructural, Construcción, Fabricación de tubos.
Aplicaciones Típicas: Juntas en T, Boquillas de soldadura en recipientes a presión, Soldaduras de filete, Soldaduras de ranura.
El detector de fallas ultrasónico WAVE con su función de plan de barrido interactivo puede optimizar significativamente la visualización de las uniones soldadas para la Inspección de Soldaduras Estructurales por AWS ya que la señal del Barrido-A se muestra a lo largo de la trayectoria del sonido, lo que permite una identificación completa de posibles ubicaciones de defectos.
Los códigos de la American Welding Society (AWS) se utilizan en Norteamérica para inspeccionar varios tipos de soldaduras en las pruebas no destructivas por ultrasonido (UT). El tipo de material soldado, el proceso de soldadura y la industria influyen directamente en los criterios de inspección.
El detector de fallas ultrasónico WAVE con su Plan de Barrido Interactivo puede optimizar significativamente la visualización de las uniones soldadas ya que la señal del Barrido A se muestra a lo largo de la trayectoria del sonido, lo que permite una identificación completa de posibles ubicaciones de defectos.
WAVE Companion, una herramienta de administración de software para PC, permite la creación de aplicaciones dedicadas (Wave App) que contienen parámetros relevantes de acuerdo con lo establecido en AWS y otros requisitos de inspección.
Características y Beneficios
- Transductores y zapatas diseñadas de acuerdo a AWS.
- Ilustraciones simples de parámetros de soldadura y juntas en T.
- Mitigar errores.
- Visualización óptima de la trayectoria del sonido en la soldadura.
- Plan de barrido interactivo para evaluación y caracterización de defectos.
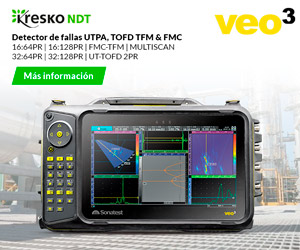
Prevención de la Corrosión en Concentrados de Partículas Magnéticas

Inspección de Puntos de Soldadura Spotweld
